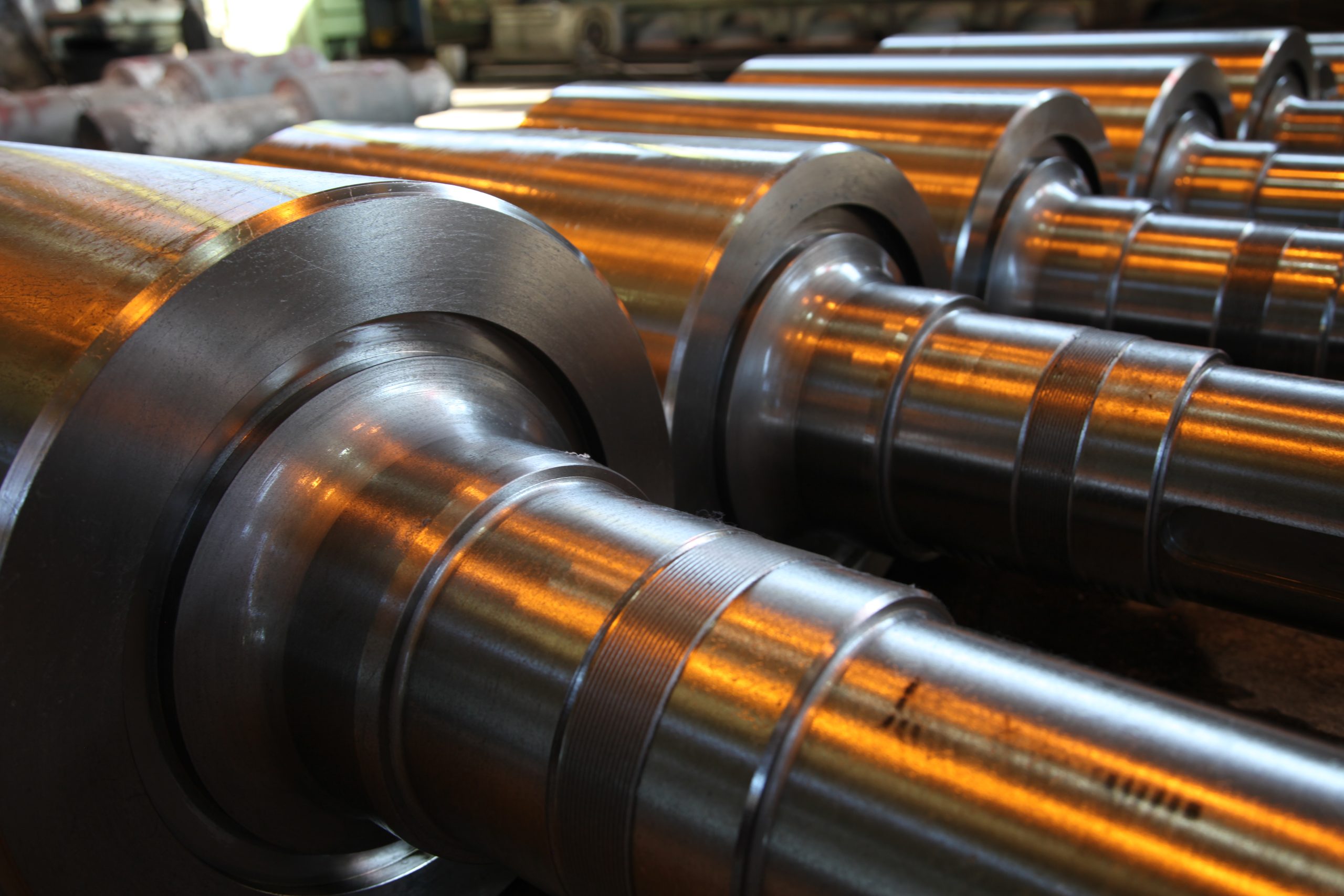
مقدمه
غلتک نورد یکی از اجزای اصلی در فرآیند نورد هستند که برای شکلدهی به فلزات و کاهش ضخامت آنها استفاده میشوند. این غلتکها در صنایع مختلف مانند فولادسازی و تولید آلومینیوم کاربرد فراوانی دارند. غلتک نورد گرم، به دلیل تحمل دمای بالا و نیروهای زیاد، از موادی مقاوم مانند چدن ساخته میشوند. در این مقاله به بررسی انواع غلتک نورد، روشهای ساخت، جنس، آنالیزهای شیمیایی و استانداردهای مرتبط با آنها میپردازیم. تمرکز اصلی بر روی غلتک نورد گرم و چدن خواهد بود.
غلتک نورد چیست؟
غلتک نورد یک استوانه فلزی است که در فرآیند نورد برای اعمال نیرو به فلز و کاهش ضخامت یا تغییر شکل آن استفاده میشود. این غلتکها به صورت مداوم در تماس با فلزات در حال نورد قرار میگیرند و از این رو باید دارای خواص مکانیکی و شیمیایی خاصی باشند که به مقاومت آنها در برابر سایش، فشار و دماهای بالا کمک کند.
انواع غلتک نورد
غلتک نورد به چندین نوع مختلف تقسیم میشوند که هر کدام برای کاربردهای خاصی در فرآیند نورد طراحی شدهاند. این تقسیمبندی عمدتاً بر اساس نوع فرآیند نورد (نورد گرم یا سرد) و جنس غلتک صورت میگیرد.
- غلتک نورد گرم:
- در نورد گرم، فلزات در دمای بالا به شکلدهی و کاهش ضخامت نیاز دارند. غلتک نورد گرم باید بتوانند دمای بالا و نیروهای زیاد را تحمل کنند. چدن یکی از مواد رایج برای ساخت این نوع غلتکها است زیرا مقاومت خوبی در برابر حرارت و سایش دارد.
- غلتک نورد سرد:
- در نورد سرد، شکلدهی فلزات در دماهای پایینتر صورت میگیرد. غلتک نورد سرد معمولاً از فولادهای سخت یا فولادهای آلیاژی ساخته میشوند تا سطح صاف و دقت بالایی را فراهم کنند.
- غلتکهای پشتیبانی:
- این غلتکها در پشت غلتکهای اصلی قرار میگیرند و وظیفه تحمل نیروی اعمال شده بر غلتکهای کاری را دارند. جنس این غلتکها معمولاً از فولاد سخت یا چدن است و باید در برابر فشارهای زیاد مقاوم باشند.
روشهای ساخت غلتک نورد
غلتک نورد به دو روش اصلی تولید میشوند: ریختهگری و ماشینکاری. این دو روش هر کدام مزایا و معایب خود را دارند و بسته به نوع غلتک و کاربرد آن، یکی از این روشها انتخاب میشود.
- ریختهگری چدن:
- چدن یکی از مواد پرکاربرد برای ساخت غلتک نورد گرم است. در فرآیند ریختهگری، مواد مذاب چدن به داخل قالبهای خاصی ریخته میشوند و پس از خنک شدن، غلتک نورد شکل میگیرند. این روش به دلیل استحکام بالا و مقاومت به سایش و حرارت چدن، بسیار رایج است.
- ماشینکاری:
- پس از ریختهگری یا برای ساخت غلتکهای دقیقتر، عملیات ماشینکاری انجام میشود. این عملیات شامل تراشکاری، سنگزنی و عملیات سطحی است تا غلتک به شکل نهایی خود برسد و سطح آن صاف و هموار شود. این فرآیند به افزایش کیفیت و دقت غلتک کمک میکند.
جنس غلتک نورد گرم
غلتک نورد گرم به دلیل شرایط سخت کاری باید از موادی ساخته شوند که بتوانند دمای بالا و فشارهای شدید را تحمل کنند. چدن یکی از پرکاربردترین مواد برای ساخت غلتک نورد گرم است. چدن به دلیل ترکیب شیمیایی خاص خود که شامل درصد بالایی از کربن و سیلیسیم است، دارای خواص مناسبی مانند مقاومت به سایش و حرارت است.
- چدن خاکستری:
- چدن خاکستری یکی از انواع چدنهای مورد استفاده در ساخت غلتک نورد است. این نوع چدن به دلیل دارا بودن گرافیت در ساختار خود، مقاومت خوبی در برابر حرارت و سایش دارد. همچنین این نوع چدن نسبت به سایر انواع چدنها از چقرمگی بالاتری برخوردار است.
- چدن داکتیل:
- چدن داکتیل یا چدن نشکن دارای استحکام و انعطافپذیری بالاتری نسبت به چدن خاکستری است. این چدن به دلیل ساختار کروی گرافیتها، توانایی تحمل فشارهای بیشتری را دارد و در برخی کاربردهای خاص نورد گرم مورد استفاده قرار میگیرد.
- فولادهای آلیاژی:
- در برخی از غلتک نورد، به خصوص غلتک نورد سرد، از فولادهای آلیاژی استفاده میشود. این فولادها مقاومت به سایش و سختی بالایی دارند و برای کاربردهایی که نیاز به دقت و سطح صاف دارند، مناسب هستند.
آنالیز شیمیایی غلتک نورد
ترکیب شیمیایی غلتک نورد باید به گونهای باشد که بتواند خواص مکانیکی و شیمیایی مناسبی را فراهم کند. آنالیز شیمیایی غلتک نورد معمولاً شامل اندازهگیری درصد عناصر اصلی مانند کربن، سیلیسیم، منگنز و سایر عناصر آلیاژی است. در ادامه به بررسی ترکیب شیمیایی غلتک نورد چدنی میپردازیم:
- کربن (C):
- کربن به عنوان یکی از عناصر اصلی در چدن، نقش مهمی در سختی و مقاومت به سایش غلتکها ایفا میکند. درصد کربن در چدن معمولاً بین 2 تا 4 درصد است.
- سیلیسیم (Si):
- سیلیسیم به بهبود مقاومت حرارتی و سایش چدن کمک میکند. درصد سیلیسیم در چدن معمولاً بین 1 تا 3 درصد است.
- منگنز (Mn):
- منگنز در ترکیب چدن باعث افزایش استحکام و مقاومت به ضربه میشود. درصد منگنز معمولاً بین 0.5 تا 1.5 درصد است.
- فسفر (P) و گوگرد (S):
- فسفر و گوگرد عموماً به عنوان عناصر نامطلوب در چدن شناخته میشوند زیرا باعث کاهش چقرمگی و مقاومت غلتک میشوند. بنابراین مقدار آنها باید در حداقل ممکن (کمتر از 0.1 درصد) باشد.
استانداردهای غلتک نورد
برای تولید و استفاده از غلتک نورد، استانداردهای مختلفی در سطح ملی و بینالمللی وجود دارند که به کیفیت و عملکرد این قطعات توجه دارند. برخی از مهمترین استانداردهای مرتبط با غلتک نورد عبارتند از:
- استانداردهای ISO:
- سازمان بینالمللی استاندارد (ISO) مجموعهای از استانداردهای جهانی برای تولید غلتک نورد تعیین کرده است. این استانداردها شامل مشخصات مربوط به ترکیب شیمیایی، روشهای تست و کنترل کیفیت غلتکها هستند.
- استاندارد ASTM:
- ASTM (American Society for Testing and Materials) یکی از معتبرترین سازمانهای استاندارد در جهان است که استانداردهای مختلفی برای غلتک نورد تدوین کرده است. این استانداردها به جنبههای مختلفی مانند خواص مکانیکی و شیمیایی و روشهای تولید میپردازند.
- استاندارد ملی ISIRI:
- در ایران، سازمان ملی استاندارد (ISIRI) نیز استانداردهایی برای تولید غلتک نورد دارد که بر ترکیب شیمیایی، خواص مکانیکی و روشهای تولید این قطعات نظارت دارد.
نتیجهگیری
غلتک نورد یکی از اجزای کلیدی در فرآیند نورد فلزات هستند که در دو نوع گرم و سرد تولید میشوند. غلتک نورد گرم به دلیل شرایط سخت کاری، از موادی مانند چدن ساخته میشوند که مقاومت به حرارت و سایش بالایی دارند. همچنین آنالیز شیمیایی دقیق و رعایت استانداردهای ملی و بینالمللی در تولید این غلتکها اهمیت فراوانی دارد. انتخاب جنس مناسب و روشهای تولید دقیق میتواند به افزایش عمر و کیفیت غلتک نورد کمک کند.